Maine
Maine needs more housing, fast. Two companies are turning to the assembly line.
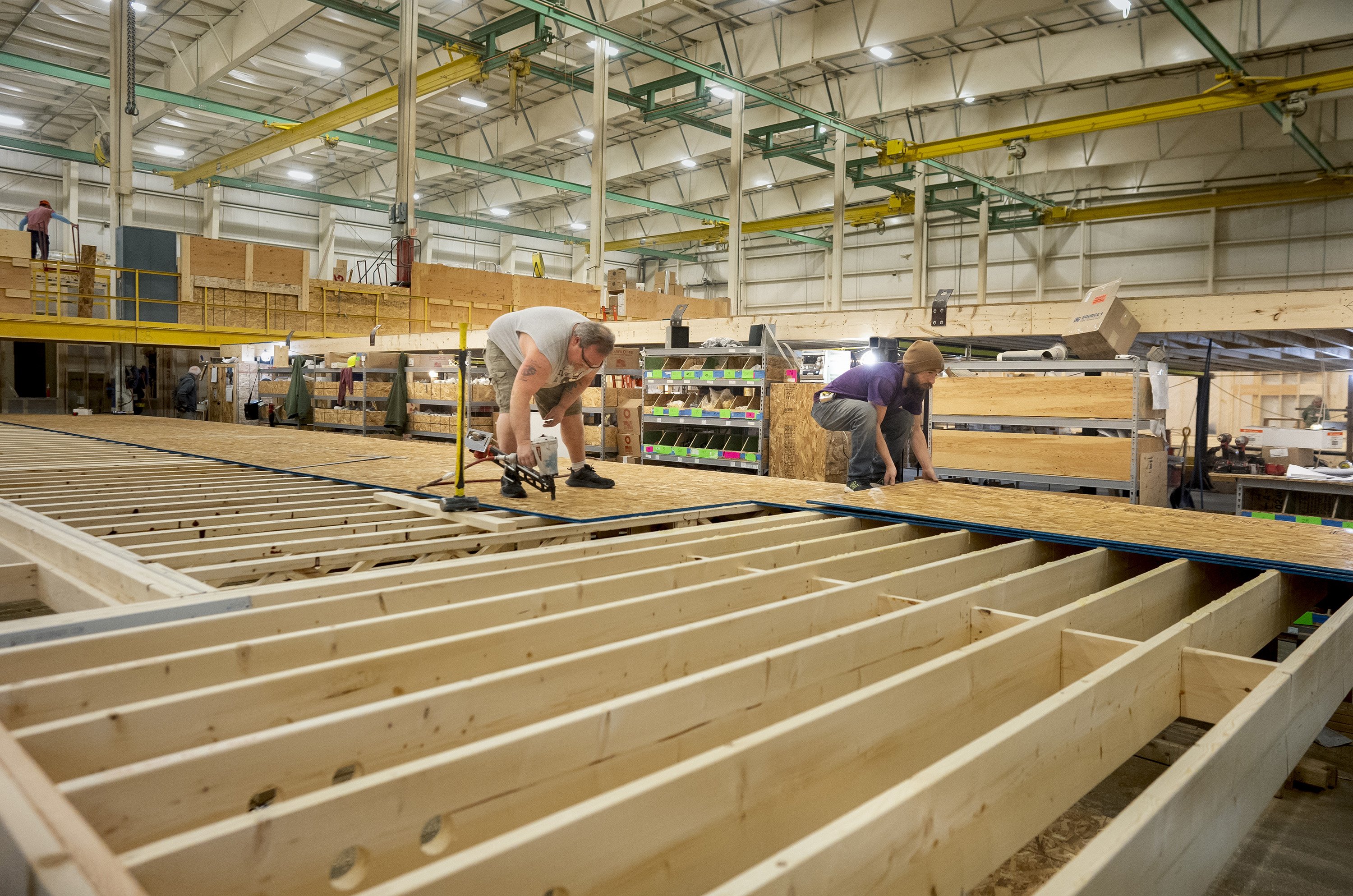
Workers at KBS Builders in South Paris work on modular components of an affordable housing complex on Dec. 13, 2024. The modular components will be trucked to Newcastle and lifted into place next week. Gregory Rec/Portland Press Herald
As more people look to lay down roots in Maine and fill critical jobs, Lincoln County is in a position where it needs to build nearly 2,000 homes in the next five years.
Washington County needs to increase its annual housing production by over 1,200%. Cumberland County is short more than 16,000 units.
Maine’s housing crisis has reached a boiling point, exacerbated by decades of underproduction.
Across the state, regulators, developers and housing advocates are scrambling to build more housing as quickly as possible to meet current and future needs.
One solution that has emerged is multifamily modular housing — an assembly-line, factory style of construction that can turn a hole in the ground into a turn-key apartment building in a matter of months, rather than the year or more required for traditional stick-built housing.
The style of building has been around for centuries but has struggled to overcome a pervasive stigma of poor quality and comparison to mobile homes.
But two Maine companies are trying to change the conversation around modular housing with multifamily buildings camouflaged as traditional New England-style homes. A flurry of projects are popping up from Sanford to Madison that, once completed, will add nearly 100 units across the state.
Dooryard, a developer and modular catalog company, and KBS Builders, a modular construction company, are spearheading the movement in Maine, which they say can not only lead to more houses in less time, but also is also labor- and cost-effective.
‘LEGO KIT OF PARTS’
Kara Wilbur, owner of Dooryard, wants to bring back the Sears and Roebuck-style catalog and is working to build one for her company with plans for anything from single-family to 20-unit buildings.
Having a “Lego kit of parts” makes it easier to go through the planning process, tweaking whatever is necessary to meet local codes, she said. The cost also goes down as elements of previous plans are reused.
Developer Kara Wilbur listens to Newcastle Town Manager Kevin Sutherland in December during a tour of KBS Builders in South Paris, where modular components of an affordable housing development were being constructed. Gregory Rec/Portland Press Herald
The factory setting can save time beyond the efficiency of an assembly line.
“You’re building in a climate-controlled environment, so the folks that are putting your house together aren’t trying to get ahead of a storm or freezing their hands off,” said Parlin Meyer, principal at BrightBuilt Home, a net-zero modular home design company in Portland that also works with KBS.
It also requires fewer people.
“Depending on the size and the scope of (a stick-built) project, you might have 20 to 30 different subcontractors on-site,” said Thatcher Butcher, president of KBS. “The builder’s biggest challenge is wrangling them and getting them to show up when they need them while getting them to show up to begin with.”
But with modular housing, 70% of the work is done in the factory, reducing the number of subcontractors needed. It allows the workers a more reliable and consistent schedule, too, providing a better work-life balance, Butcher said.
DOZENS OF UNITS IN THE PIPELINE
Wilbur, along with partners Brian Eng and Sam Hight, launched the affordable housing modular model in Madison with 18 apartments in two buildings reserved for people making 80% of the area median income. They broke ground in October 2023 and tenants moved in seven months later. Another 18-unit project is awaiting funding.
Wilbur hopes to replicate the process with similar projects planned for Rumford and, following planning board approval Wednesday, Yarmouth.
Workers at KBS Builders in South Paris work on modular components of an affordable housing complex on Dec. 13, 2024. Gregory Rec/Portland Press Herald
In Sanford, Wilbur is partnering with MaineHousing to try out a modular development for prospective homeowners, rather than renters. The project includes nine condos and one single-family home on a lot near the city’s former mill buildings. The condos are reserved for people making 120% of the area median income, and the pre-sale process is underway.
While those are still in the early stages, developer Rob Nelson is nearing the next stage on a project in Newcastle.
The Midcoast town, sandwiched between the Damariscotta and Sheepscot rivers, has a population of fewer than 2,000 people. Nelson wanted to make sure that the two-building, 16-unit project, which is within walking distance of the village center, blended in with the community.
“A 50-unit project would be hard to make work in a town like Newcastle. The smaller project fit better with the community,” he said. “A year from now, when people drive down the street, they’ll think they’ve always been there.”
Kevin Sutherland, town manager of Newcastle, inspects a modular component being built at KBS Builders in South Paris last December. Gregory Rec/Portland Press Herald
The building uses the same model as the Madison project. Crews broke ground in late October. The modules will be installed next week, and Nelson hopes to have the buildings ready for occupancy in the spring.
The units will be reserved for people making 80% or less of the area median income. Rent will be about $1,400 a month for a one-bedroom.
“That is by no means cheap, but it’s filling a need in the market,” he said.
LACK OF HOUSING AN ‘EXISTENTIAL THREAT’
Nelson’s project could serve as an example to other communities in Lincoln County — and elsewhere — that are desperate for more affordable housing, said Emily Rabbe, executive director of the Lincoln County Regional Planning Commission.
“The potential for these modular units to be able to speed up construction, maintain the affordability of the unit and make it work from a development perspective to me feels like it’s critical,” she said. “We’re in a housing crisis now, and to have to wait another two to three years before we have units that are move-in ready is a really hard thing to tell people when they need a home today.”
The median sale price for a home in Lincoln County has climbed 127% in the last five years, more than any other county. Comparatively, the statewide median has risen 77%.
In 2023, the median sale price in Lincoln County was $440,000, a price that according to MaineHousing, was unaffordable to almost 90% of the population. By November 2024, the price had increased to $510,000.
Gerry Howley of KBS Builders, left, points out a detail to Kara Wilbur and Rob Nelson inside one of the modular components for an affordable housing development that will be constructed in Newcastle. Gregory Rec/Portland Press Herald
The 16 units from Nelson’s project in Newcastle, coupled with at least 40 units of modular housing (part of a larger, 136-unit development) headed for nearby Boothbay, seem like a drop in the bucket, but they’re a start. Modular housing can’t solve all the problems, but Rabbe said these projects can play a key role as Lincoln County evaluates its future.
For one of the oldest counties in the nation’s oldest state, affordability is key to simply keeping the economy up and running – let alone growing it – when an anticipated 19% of the workforce retires in the next 10 years. That new workforce needs homes to live in and the retiring workers will likely need homes they can manage on a fixed income.
A study commissioned last year by MaineHousing found that the area’s workforce housing shortage poses an “existential threat” to the region’s economic future.
“The housing issue is so multifaceted and the need is so dire,” Rabbe said. “No action is not an option for Lincoln County.”
AESTHETICS KEY TO FIGHTING STIGMA
While modular construction has been around for centuries, it really took off in the early 1900s when Sears and Roebuck began selling mail-order catalog homes by the tens of thousands.
Still, it only represents about 3% of the country’s residential construction and just 1% of new multifamily homes.
This is in stark contrast to other countries like Finland, Norway and Sweden, where 45% of homes are modular, and Japan, where modular housing represents 15% of construction, according to the Center for American Progress.
A rendering of the modular eight-unit condo building and single-family home on Bodwell Street in Sanford. Rendering by Dooryard and New Paradigm Design Workshop
Butcher chalks the reticence up to stigma – and it’s the biggest hurdle he sees to widespread adoption.
“I think a lot of it is largely driven by the way that the U.S. pursued HUD-style mobile homes back throughout the ’60s, ’70s, and ’80s, and unfortunately that product was low-quality and low-performance,” Butcher said. “It gave modular and offsite housing a bad name, and those two (modular and mobile homes) have become synonymous in people’s minds. Our biggest challenge is unwrapping those two and unpackaging them and getting people to see that modular housing is not mobile homes.”
Wilbur said that making the buildings blend in with their surroundings is key to reshaping those perceptions, which is why most of her developments are modeled after the traditional “New England village aesthetic” with pitched roofs, bay windows and front porches.
She wants to showcase that modular housing can be more attractive than “off-the-shelf ranch-style” homes, while still being compact and energy-efficient.
“It makes the most sense to put housing in our village downtowns,” she said, “so if we want to get community buy-in around new development in general, we have to do a good job designing projects. They’re beloved places in communities so the bar is set a lot higher.”
FUNDING STILL NECESSARY
While the approach is in many ways less costly for developers, it’s still expensive, especially at smaller scales of under 20 units, where it’s generally not feasible to use low-income housing tax credits.
A program from MaineHousing, the Rural Affordable Rental Housing program, aims to help by providing funding to developers of five- to 18-unit projects of affordable housing in rural areas.
Hight, co-developer on the Madison project, said the financing from MaineHousing was “completely necessary for anyone in their right mind to take on a project like this.”
Gerry Howley of KBS Builders, left, talks with Kara Wilbur and Rob Nelson inside one of the modular components at KBS in South Paris. Gregory Rec/Portland Press Herald
Building materials are expensive no matter how a house gets built.
“The only options are subsidized projects or luxury projects, and there are only so many places in Maine that could even support that,” Wilbur said. “It’s why the Rural Affordable Rental Program is critical because it is, in rural Maine, one of the only sources of funding available.”
So far, all five developments have either received or have applied for financing from MaineHousing, but Wilbur said she hopes to make traditional financing viable for future projects without having to sacrifice quality.
Dooryard and KBS are also working on conceptual models for multifamily housing projects that would align with federal Low-Income Housing Tax Credit standards, which might appeal to larger developers.
“There’s not one silver bullet that’s going to solve the housing crisis,” said Meyer, at Brightbuilt. “(But) I think modular is absolutely a piece of the puzzle, and it’s one that can help solve the need in a shorter timeline.”